ヒケの制御
IMP工法により外観不良のヒケを抑制できます。
ヒケは寸法精度を悪化させる主な要因であり、外観不良でもあります。
PLAMOで行っているIMP工法では、充填圧力を必要とする部位のみ掛けることが出来るため、ヒケに対して高い効果が得られ、射出工程以上に高い保圧効果を発揮し高精度安定を実現します。
(IMP工法:イン・モールド・プレッシング工法の略)
(IMP工法は当社独自開発による加工方法です)
ヒケのお困りごとを解決します!
- 成形条件をいろいろ試したがヒケの改善が限定的である。
- ヒケを抑えるのに成形サイクルが長くなる。
- ヒケを抑えるために射出圧力を上げるとバリが発生する。
このようなヒケに効果を発揮します
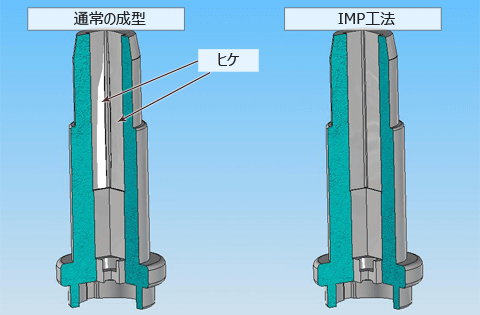
例)この様な形状の場合、内壁のヒケが発生し寸法精度を損ねます。金型の補正対応も限定的であり、IMP工法によりヒケの無い高精度な製品をご提供します。
IMP工法によるヒケ制御成形
ヒケは寸法精度向上と同じく、充填圧力不足が主な要因です。
通常成形での対策として射出圧力を高め、射出速度を低め、ゲートシールを遅らせるために金型温度を上げたりゲート面積を大きくしたりといった対策を講じますが、どれも成形サイクルを長期化させることになります。また、偏肉製品の様に充填圧力の均一が図れない製品形状においては対策案は限られます。
当社のIMP工法は充填圧力を必要とする部位のみ掛けることが出来るため、ヒケに対して高い効果が得られます。
IMP工法による高精度実現提案
IMP工法は射出工程以上に高い保圧効果を発揮し高精度安定を実現します。
測定サンプルと測定結果のグラフを表しました。
下記写真は肉厚12mmを有する偏肉成形品です。通常成形ではヒケ量が最大で0.38mmの結果に。IMP工法ではヒケ量を0.06mmまで抑えた改善効果がみられます。
通常成形とIMMP工法 キャビティ内圧の測定結果
下図はキャビティ内圧を測定した結果です。
IMP工法の充填圧力メカニズムを表しました。(横軸:射出開始からの経過時間 縦軸:キャビティ内圧)
通常成形の場合、射出開始より内圧が62MPaに上昇し、そこから熱収縮とあわせて内圧が徐々に低下しています。50SECにて内圧はゼロとなります。内圧ゼロとはキャビティ面より製品表面が離れたことを意味し、ヒケが発生していることを意味しています。
対してIMP工法は通常成形の射出と同じ波形を駆動開始まで辿りますが、駆動開始より内圧が更に高まり35SEC時点で120MPaまで高まっています。その後、熱収縮により通常成形と同様に内圧は低下していきますが、内圧がゼロとなる時間は通常成形とは大きく異なり120SECまで到達します。
IMP工法の利点として
- 通常成形では実現できない高い充填圧力が得られる。
- IMP工法駆動条件により開始時刻を遅らせることが出来る。
- IMP工法駆動条件によりピーク圧を制御出来る。
- IMP工法駆動条件によりピーク時間を遅らせることが出来る。
通常成形の場合、IMP工法と同等の充填圧力を出すためには高い射出圧力と射出速度が必要となり、オーバーパック(パーティングが開く)によるバリの発生原因となります。 IMP工法では製品スキン層が十分に形成(固化)した段階より圧縮を開始できるためにバリの発生を抑えながらヒケを抑えることが容易です。
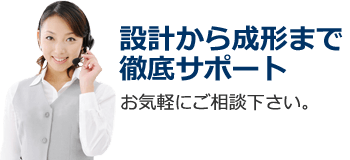